مصرف انرژی در تولید سیمان و راه های بهینه سازی
صنعت سیمان به عنوان یکی از ستون های اصلی توسعه زیرساخت ها در سراسر جهان متأسفانه در فهرست پرمصرف ترین صنایع از نظر انرژی قرار دارد. این مصرف بالای انرژی نه تنها هزینه های تولید را به شدت تحت تأثیر قرار می دهد بلکه پیامدهای زیست محیطی قابل توجهی از جمله انتشار مقادیر زیادی گازهای گلخانه ای به ویژه دی اکسید کربن (CO2) به همراه دارد. اهمیت بهینه سازی مصرف انرژی در این صنعت حیاتی است؛ چرا که دستیابی به توسعه پایدار کاهش اثرات مخرب زیست محیطی و افزایش تاب آوری اقتصادی کارخانجات سیمان مستلزم مدیریت بهینه منابع انرژی است. این مقاله به واکاوی دقیق چالش های مرتبط با مصرف انرژی در فرآیند تولید سیمان پرداخته و راهکارهای مؤثر و فناورانه را برای کاهش آن ارائه می دهد.
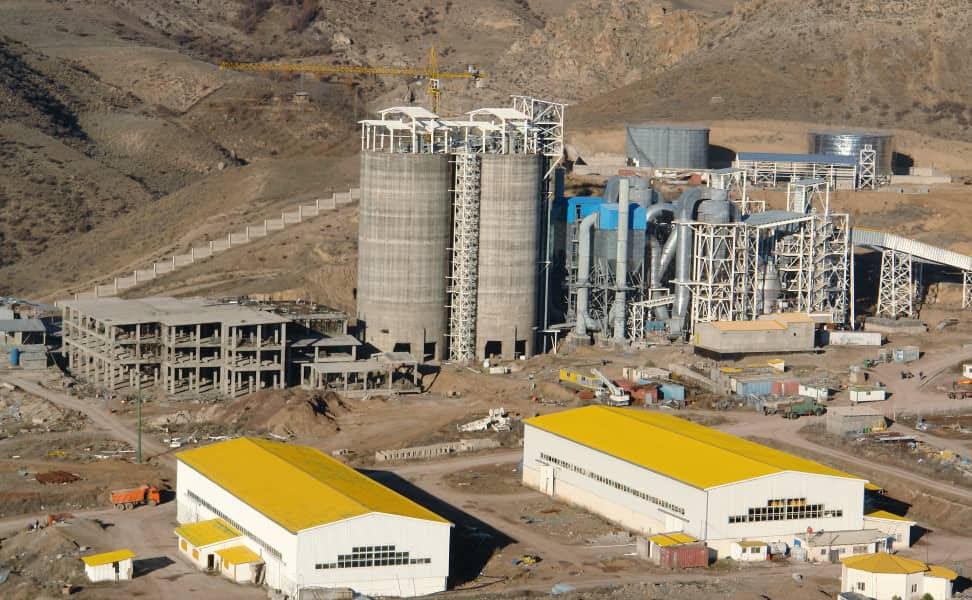
تمرکز بر بهینه سازی مصرف انرژی در صنعت سیمان فراتر از یک اقدام صرفاً اقتصادی است؛ این یک ضرورت استراتژیک برای بقا و رقابت پذیری در بازارهای جهانی است که به طور فزاینده ای به سمت اقتصاد سبز و مسئولیت اجتماعی حرکت می کنند. شناخت دقیق نقاط پرمصرف انرژی در هر مرحله از تولید گام نخست در تدوین استراتژی های مؤثر برای کاهش مصرف و هزینه هاست. این امر نیازمند تحلیل سیستماتیک فرآیندها به کارگیری فناوری های پیشرفته و اجرای برنامه های مدیریت انرژی جامع است. برای استعلام قیمت سیمان تهران در الومتریال به صورت هفتگی پیگیر ارتباط با این مجموعه باشید تا به روزترین قیمت ها را در اختیار شما قرار دهند.
فرآیند تولید سیمان و نقاط پرمصرف انرژی
تولید سیمان یک فرآیند پیچیده و چندمرحله ای است که از استخراج مواد اولیه آغاز شده و با بسته بندی محصول نهایی پایان می یابد. هر یک از این مراحل نیازمند صرف انرژی قابل توجهی است اما سهم هر مرحله در کل مصرف انرژی متفاوت است. درک این تفاوت ها برای شناسایی اولویت های بهینه سازی ضروری است.
به طور کلی دو نوع عمده انرژی در صنعت سیمان مصرف می شود: انرژی حرارتی (معمولاً از طریق احتراق سوخت ها) و انرژی الکتریکی. سهم انرژی حرارتی به طور معمول بسیار بیشتر از انرژی الکتریکی است و بخش عمده آن در مرحله پخت کلینکر مصرف می شود.
استخراج و آماده سازی مواد اولیه
مرحله اولیه تولید سیمان شامل استخراج مواد خام اصلی مانند سنگ آهک رس مارل بوکسیت و سنگ آهن از معادن است. پس از استخراج این مواد به کارخانه منتقل شده و تحت عملیات خردایش و آسیاب قرار می گیرند تا به اندازه دانه بندی مناسب برای ورود به کوره برسند. این مرحله شامل فعالیت هایی نظیر حفاری بارگیری حمل و نقل خردایش اولیه و ثانویه و آسیاب کردن است.
انرژی مصرفی در این مرحله عمدتاً به صورت انرژی الکتریکی برای راه اندازی ماشین آلات سنگین معدنی سیستم های نقاله سنگ شکن ها (مانند سنگ شکن فکی کوبیت مخروطی) و آسیاب های مواد خام (مانند آسیاب گلوله ای یا آسیاب عمودی غلتکی – VRM) است. اگرچه سهم این مرحله در کل مصرف انرژی کمتر از مرحله پخت است اما بهینه سازی در این بخش نیز می تواند به کاهش هزینه ها و بهبود کلی راندمان انرژی کارخانه کمک کند. استفاده از تجهیزات با راندمان بالا و بهینه سازی مسیرهای حمل و نقل از جمله راهکارهای مؤثر در این مرحله محسوب می شود.
پخت کلینکر: قلب پرمصرف فرآیند
مرحله پخت کلینکر بدون شک پرمصرف ترین بخش در فرآیند تولید سیمان است و بیشترین سهم انرژی حرارتی را به خود اختصاص می دهد. در این مرحله مخلوط مواد خام آسیاب شده (خوراک کوره) وارد کوره دوار می شود و در دماهای بسیار بالا (حدود ۱۴۵۰ درجه سانتی گراد در منطقه پخت) حرارت می بیند.
در طول عبور خوراک از کوره واکنش های شیمیایی پیچیده ای رخ می دهد که مهم ترین آن ها کلسیناسیون (تجزیه کربنات کلسیم به اکسید کلسیم و CO2) و کلینکرسازی (تشکیل فازهای اصلی کلینکر مانند آلیت بلیت فریت و سلرایت) است. این واکنش ها گرماگیر بوده و نیازمند تأمین انرژی حرارتی بسیار زیادی هستند. سوخت اصلی مورد استفاده در کوره های سیمان به طور سنتی سوخت های فسیلی مانند زغال سنگ کک نفتی (پت کک) گاز طبیعی یا مازوت است. راندمان پایین انتقال حرارت در کوره های قدیمی اتلاف حرارت از بدنه کوره و گرمای تلف شده در گازهای خروجی و کلینکر داغ از عوامل اصلی مصرف بالای انرژی در این مرحله هستند. مصرف ویژه انرژی حرارتی در این مرحله معمولاً بین ۷۵۰ تا ۹۰۰ کیلوکالری بر کیلوگرم کلینکر متغیر است که نشان دهنده پتانسیل بالای صرفه جویی است.
آسیاب سیمان و بسته بندی
پس از خروج کلینکر از کوره و خنک شدن آن را با مقادیر کمی سنگ گچ و سایر مواد افزودنی (مانند پوزولان ها سرباره کوره بلند یا خاکستر بادی) مخلوط کرده و در آسیاب های سیمان مجدداً آسیاب می کنند تا به پودر بسیار نرمی تبدیل شود که همان سیمان پرتلند است. این مرحله نیز نیازمند مصرف قابل توجهی انرژی است که عمدتاً به صورت انرژی الکتریکی برای راه اندازی آسیاب ها (مانند آسیاب گلوله ای آسیاب عمودی غلتکی یا رولر پرس همراه با آسیاب گلوله ای) سپراتورها (جداکننده ها) فن ها و سیستم های انتقال مواد مصرف می شود.
میزان مصرف انرژی الکتریکی در این مرحله به نوع آسیاب نرمی سیمان مورد نیاز و خواص کلینکر بستگی دارد و می تواند بین ۳۰ تا ۵۰ کیلووات ساعت بر تن سیمان متغیر باشد. پس از آسیاب سیمان در سیلوها ذخیره شده و سپس در کیسه یا به صورت فله بسته بندی و بارگیری می شود. انرژی مصرفی در مرحله بسته بندی و بارگیری نسبت به مراحل قبلی کمتر است و شامل انرژی الکتریکی برای ماشین آلات بسته بندی سیستم های نقاله و پمپ های هوای فشرده است. بهینه سازی در این مرحله نیز شامل استفاده از تجهیزات با راندمان بالا و کاهش ضایعات انرژی است.
راهکارهای بهینه سازی مصرف انرژی در تولید سیمان
کاهش مصرف انرژی در صنعت سیمان نیازمند رویکردی جامع و چندوجهی است که تمامی مراحل فرآیند تولید را در بر گیرد. اجرای راهکارهای مؤثر می تواند به کاهش هزینه های تولید افزایش بهره وری و بهبود عملکرد زیست محیطی کارخانه منجر شود.
بهبود راندمان کوره های پخت کلینکر
از آنجا که مرحله پخت کلینکر بیشترین سهم را در مصرف انرژی حرارتی دارد بهبود راندمان کوره ها از اولویت های اصلی بهینه سازی است. راهکارهای کلیدی در این زمینه عبارتند از:
- استفاده از پیش گرمکن های چندمرحله ای سیکلونی: این سیستم ها با استفاده از حرارت گازهای خروجی کوره خوراک خام را قبل از ورود به کوره پیش گرم می کنند و راندمان انتقال حرارت را به طور چشمگیری افزایش می دهند. پیش گرمکن های چهار پنج یا شش مرحله ای نسبت به سیستم های قدیمی تر راندمان بالاتری دارند.
- استفاده از پیش کلسینر: در کوره های دارای پیش کلسینر بخش قابل توجهی از واکنش کلسیناسیون (حدود ۹۰-۹۵ درصد) در خارج از کوره و در محفظه پیش کلسینر انجام می شود. این امر بار حرارتی کوره را کاهش داده و امکان استفاده بیشتر از سوخت های جایگزین را فراهم می کند.
- بازیافت حرارت از کلینکر داغ: کلینکر پس از خروج از کوره دمای بسیار بالایی دارد. استفاده از سیستم های خنک کننده کلینکر (مانند گریت کولر) که حرارت کلینکر را بازیافت کرده و هوای احتراق را پیش گرم می کنند راندمان حرارتی فرآیند را به طور قابل ملاحظه ای افزایش می دهد.
- بهینه سازی سیستم سوخت رسانی و مشعل: طراحی مناسب مشعل و کنترل دقیق نسبت هوا به سوخت احتراق کامل تر و راندمان بالاتری را تضمین می کند.
- عایق بندی مناسب کوره و سیستم های مرتبط: کاهش اتلاف حرارت از بدنه کوره داکت ها و سایر تجهیزات از طریق عایق بندی مؤثر.
- کنترل پیشرفته فرآیند (APC): استفاده از سیستم های کنترلی خودکار و پیشرفته که پارامترهای کلیدی فرآیند مانند دما فشار و ترکیب گازهای خروجی را به طور پیوسته پایش و تنظیم می کنند به پایداری فرآیند و کاهش مصرف انرژی کمک می کند. جهت مشاهده ویدئوهایی که شما را با روند تولید کلینیکر اشنا می کند به یوتیوپ مراجعه کنید.
استفاده از سوخت های جایگزین و انرژی های تجدیدپذیر
جایگزینی بخشی از سوخت های فسیلی با سوخت های جایگزین (Alternative Fuels – AFs) یکی از مؤثرترین راهکارها برای کاهش هزینه ها و انتشار گازهای گلخانه ای در صنعت سیمان است. این سوخت ها می توانند شامل موارد زیر باشند:
- ضایعات کشاورزی: مانند پوست برنج کاه و کلش.
- پسماندهای شهری و صنعتی: مانند RDF (سوخت مشتق شده از زباله) پلاستیک ها لاستیک های فرسوده لجن فاضلاب.
- پسماندهای زیستی: مانند روغن های پخت و پز مستعمل ضایعات چوب.
استفاده از این سوخت ها نیازمند آماده سازی مناسب (خردایش خشک کردن همگن سازی) و همچنین کنترل دقیق انتشار آلاینده ها است. نرخ جایگزینی سوخت های فسیلی با AFs در کارخانجات پیشرفته می تواند به بیش از ۸۰ درصد برسد.
علاوه بر سوخت های جایگزین استفاده از انرژی های تجدیدپذیر مانند انرژی خورشیدی (برای تأمین بخشی از برق مصرفی) و انرژی بادی نیز می تواند در کاهش وابستگی به سوخت های فسیلی و کاهش انتشار CO2 مؤثر باشد هرچند سهم این منابع در تأمین انرژی حرارتی کوره محدودتر است.
بهینه سازی سیستم های آسیاب و خردایش
مرحله آسیاب کردن مواد خام و کلینکر مصرف کننده اصلی انرژی الکتریکی در کارخانه سیمان است. بهبود راندمان در این بخش از اهمیت بالایی برخوردار است:
- استفاده از آسیاب های با راندمان بالا: آسیاب های عمودی غلتکی (VRM) و رولر پرس ها (HPGR) نسبت به آسیاب های گلوله ای سنتی به طور قابل توجهی انرژی کمتری برای آسیاب کردن هر تن مواد مصرف می کنند. جایگزینی یا به روزرسانی آسیاب های قدیمی با این فناوری های جدید می تواند صرفه جویی قابل توجهی در مصرف برق ایجاد کند.
- بهینه سازی مدار آسیاب: تنظیم مناسب سپراتورها برای کنترل دقیق اندازه ذرات استفاده از سیکلون های با راندمان بالا و بهینه سازی جریان مواد در مدار آسیاب.
- استفاده از افزودنی های آسیاب (Grinding Aids): این مواد شیمیایی با کاهش تجمع ذرات در داخل آسیاب و کاهش انرژی سطحی فرآیند آسیاب را تسهیل کرده و باعث کاهش مصرف انرژی و افزایش ظرفیت آسیاب می شوند.
- نگهداری و تعمیرات پیشگیرانه: اطمینان از وضعیت مناسب قطعات آسیاب (مانند لاینرها گلوله ها غلتک ها) و سپراتورها برای حفظ راندمان عملیاتی.
- بهینه سازی اندازه خوراک ورودی به آسیاب: انجام پیش خردایش مؤثر قبل از ورود مواد به آسیاب اصلی می تواند بار روی آسیاب را کاهش داده و مصرف انرژی را پایین بیاورد.
مدیریت انرژی و ممیزی انرژی
اجرای یک سیستم مدیریت انرژی مدون و انجام ممیزی های انرژی دوره ای اساس شناسایی و اجرای فرصت های بهینه سازی انرژی در کل کارخانه است. مدیریت انرژی شامل مجموعه ای از فعالیت ها برای پایش تحلیل و کنترل مصرف انرژی است:
- استقرار سیستم مدیریت انرژی (مانند ISO 50001): این استاندارد چارچوبی برای بهبود مستمر عملکرد انرژی فراهم می کند.
- ممیزی انرژی: فرآیند سیستماتیک جمع آوری داده های مصرف انرژی تحلیل آن ها شناسایی نقاط اتلاف انرژی و ارائه راهکارهای صرفه جویی. ممیزی می تواند شامل ممیزی اولیه ممیزی تفصیلی و ممیزی هدفمند برای تجهیزات خاص باشد.
- نصب تجهیزات اندازه گیری (کنتورها): نصب کنتورهای انرژی (الکتریکی و حرارتی) در نقاط کلیدی فرآیند برای پایش دقیق مصرف و شناسایی الگوهای مصرف.
- تعیین شاخص های عملکرد انرژی (EnPIs): تعریف و پایش شاخص هایی مانند مصرف ویژه انرژی حرارتی (کیلوکالری بر کیلوگرم کلینکر یا سیمان) و مصرف ویژه انرژی الکتریکی (کیلووات ساعت بر تن سیمان) برای مقایسه عملکرد در دوره های مختلف و ارزیابی اثربخشی اقدامات بهینه سازی.
- آموزش کارکنان: افزایش آگاهی و دانش کارکنان در خصوص اهمیت بهینه سازی انرژی و نقش آن ها در اجرای راهکارها.
- بازیابی حرارت تلف شده (WHR): در برخی کارخانجات پیشرفته از حرارت تلف شده در گازهای خروجی کوره و خنک کننده کلینکر برای تولید برق استفاده می شود که می تواند بخش قابل توجهی از نیاز الکتریکی کارخانه را تأمین کند.
مزایای اقتصادی و زیست محیطی بهینه سازی مصرف انرژی
بهینه سازی مصرف انرژی در صنعت سیمان منافع گسترده ای را به همراه دارد که هم شامل مزایای اقتصادی مستقیم برای تولیدکننده و هم مزایای زیست محیطی برای جامعه و کره زمین می شود.
مزایای اقتصادی:
- کاهش هزینه های تولید: انرژی یکی از بزرگترین سرفصل های هزینه ای در تولید سیمان است. کاهش مصرف انرژی به طور مستقیم منجر به کاهش هزینه های سوخت و برق شده و سودآوری کارخانه را افزایش می دهد.
- افزایش رقابت پذیری: کاهش هزینه های تولید به کارخانجات سیمان اجازه می دهد محصولات خود را با قیمت رقابتی تری عرضه کنند.
- بهبود بهره وری: اغلب راهکارهای بهینه سازی انرژی مانند به روزرسانی تجهیزات یا بهبود کنترل فرآیند منجر به افزایش بهره وری کلی خط تولید نیز می شوند.
- کاهش ریسک ناشی از نوسانات قیمت انرژی: وابستگی کمتر به سوخت های فسیلی و استفاده از منابع انرژی متنوع تر (مانند سوخت های جایگزین) ریسک ناشی از نوسانات قیمت انرژی را کاهش می دهد.
- دسترسی به مشوق ها و تسهیلات دولتی: در بسیاری از کشورها دولت ها برای تشویق صنایع به کاهش مصرف انرژی و انتشار آلاینده ها مشوق های مالیاتی وام های کم بهره یا کمک های بلاعوض ارائه می دهند.
مزایای زیست محیطی:
- کاهش انتشار گازهای گلخانه ای (به ویژه CO2): بخش عمده انتشار CO2 در صنعت سیمان ناشی از کلسیناسیون سنگ آهک و احتراق سوخت های فسیلی است. بهینه سازی مصرف انرژی حرارتی و استفاده از سوخت های جایگزین کربن خنثی یا کم کربن به طور مستقیم انتشار CO2 ناشی از احتراق را کاهش می دهد.
- کاهش انتشار سایر آلاینده ها: بهبود فرآیند احتراق و استفاده از سوخت های جایگزین مناسب می تواند به کاهش انتشار اکسیدهای نیتروژن (NOx) اکسیدهای گوگرد (SOx) و ذرات معلق نیز کمک کند.
- حفظ منابع طبیعی: کاهش مصرف سوخت های فسیلی به حفظ این منابع محدود برای نسل های آینده کمک می کند.
- مدیریت بهتر پسماندها: استفاده از پسماندها به عنوان سوخت جایگزین به حل مشکل دفع این مواد کمک کرده و نیاز به دفن زباله را کاهش می دهد.
- بهبود کیفیت هوا و آب: کاهش انتشار آلاینده ها تأثیر مستقیمی بر بهبود کیفیت هوا و آب در اطراف کارخانجات و مناطق مسکونی دارد.
در مجموع سرمایه گذاری در بهینه سازی مصرف انرژی در صنعت سیمان یک استراتژی برد-برد است که هم منافع اقتصادی ملموسی برای صنعتگران به همراه دارد و هم به حفاظت از محیط زیست و دستیابی به اهداف توسعه پایدار کمک می کند.
چگونه می توان راندمان کوره های پخت کلینکر را افزایش داد؟
راندمان کوره ها با استفاده از پیش گرمکن ها و پیش کلسینرها بازیافت حرارت کلینکر بهینه سازی مشعل عایق بندی مناسب و کنترل پیشرفته فرآیند بهبود می یابد.
چه سوخت های جایگزینی می توان در تولید سیمان استفاده کرد؟
می توان از ضایعات کشاورزی پسماندهای شهری و صنعتی مانند RDF و لاستیک های فرسوده و پسماندهای زیستی استفاده کرد.
نقش دولت در تشویق به بهینه سازی مصرف انرژی در صنعت سیمان چیست؟
دولت می تواند با ارائه مشوق های مالیاتی وام های کم بهره کمک های بلاعوض و وضع قوانین و استانداردها صنایع را به سمت بهینه سازی مصرف انرژی سوق دهد.
مزایای استفاده از سیمان های کم کربن چیست؟
سیمان های کم کربن با کاهش سهم کلینکر در محصول نهایی و استفاده از مواد افزودنی انتشار CO2 در فرآیند تولید را کاهش داده و به پایداری بیشتر کمک می کنند.
چگونه می توان مصرف انرژی در آسیاب سیمان را کاهش داد؟
با استفاده از آسیاب های با راندمان بالا (VRM رولر پرس) بهینه سازی مدار آسیاب استفاده از افزودنی های آسیاب و نگهداری مناسب تجهیزات می توان مصرف انرژی الکتریکی را کاهش داد.
آیا شما به دنبال کسب اطلاعات بیشتر در مورد "مصرف انرژی در تولید سیمان و راه های بهینه سازی" هستید؟ با کلیک بر روی اقتصادی, کسب و کار ایرانی، آیا به دنبال موضوعات مشابهی هستید؟ برای کشف محتواهای بیشتر، از منوی جستجو استفاده کنید. همچنین، ممکن است در این دسته بندی، سریال ها، فیلم ها، کتاب ها و مقالات مفیدی نیز برای شما قرار داشته باشند. بنابراین، همین حالا برای کشف دنیای جذاب و گسترده ی محتواهای مرتبط با "مصرف انرژی در تولید سیمان و راه های بهینه سازی"، کلیک کنید.